Confidential Client
Read More
CapEx validation study saves $2.5 MM in CIP equipment
CSL Seqirus, a global producer of influenza vaccines, was on a mission to increase production. After receiving a design recommending three new clean-in-place (CIP) skids at $5 million to facilitate the increase, Seqirus’s team engaged CRB’s consulting services to conduct a validation study. Their team wanted to perform the proper due diligence to ensure the proposed equipment was necessary before moving forward with the project and investment.
Project Details
Client
CSL Seqirus
Verifying the need for new CIP equipment
To answer Seqirus’ question, our team developed a process model and ran several simulations to understand how the existing CIP equipment and systems could be reassigned and optimized. When a simulation returned promising results, the design was then verified internally by a CRB biopharma process engineer for real-world viability. This iterative and collaborative process helped ensure our data-driven outcomes were checked against industry experience, identifying the best options for both CapEx and practical operations.
The process simulation outcome
In the end, our team presented three viable CIP scenarios at various degrees of process optimization to offer the client choice and flexibility in their design. The final recommendation cut the capital expense in half and reduced the equipment scope from three CIP skids to just one.
The project team’s due diligence paid off:
- Reduced design from 3 CIP skids to 1 CIP skid
- Reduced CapEx from $5 million to $2.5 million
- Increase in throughput
- Confidence in the investment
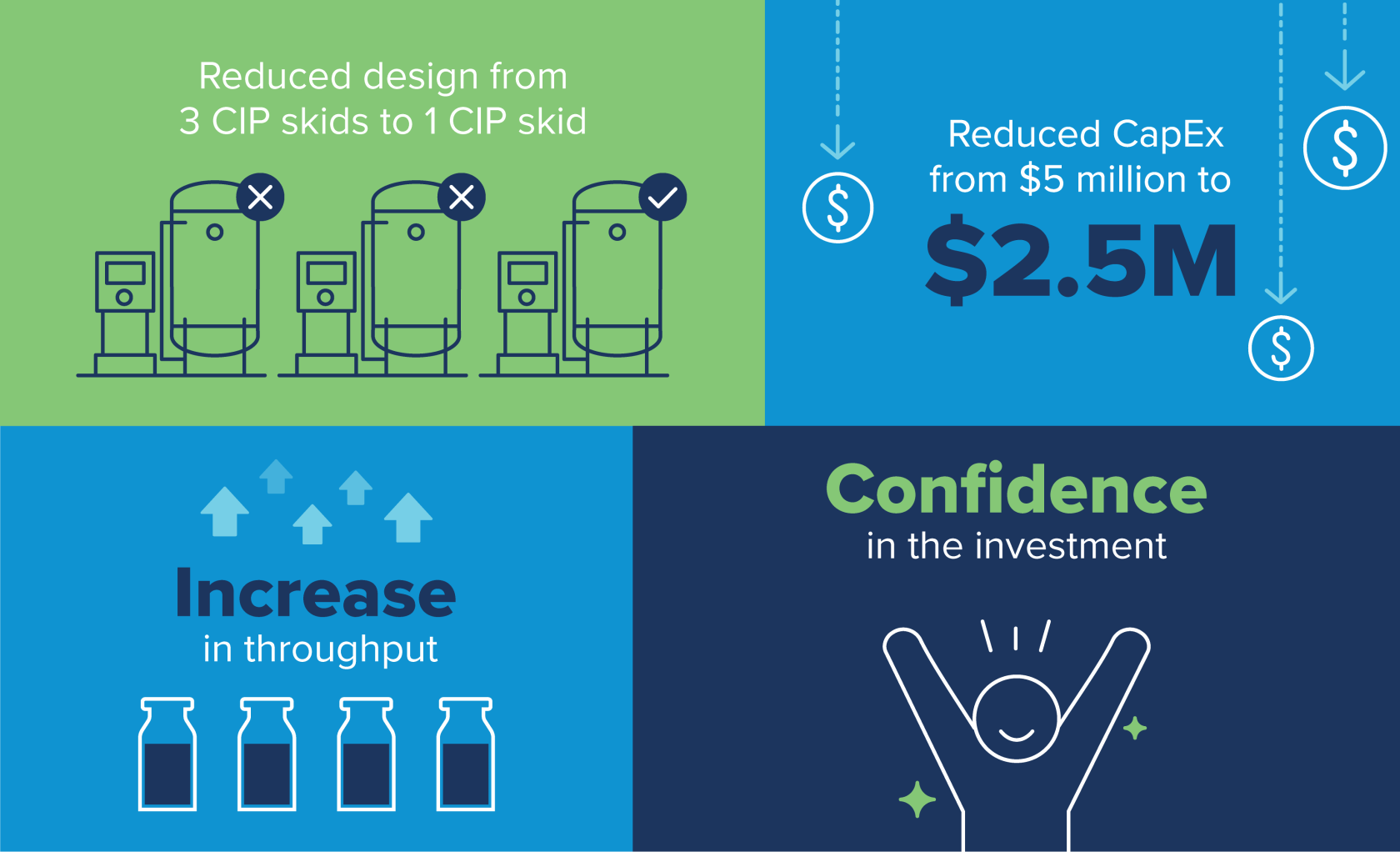
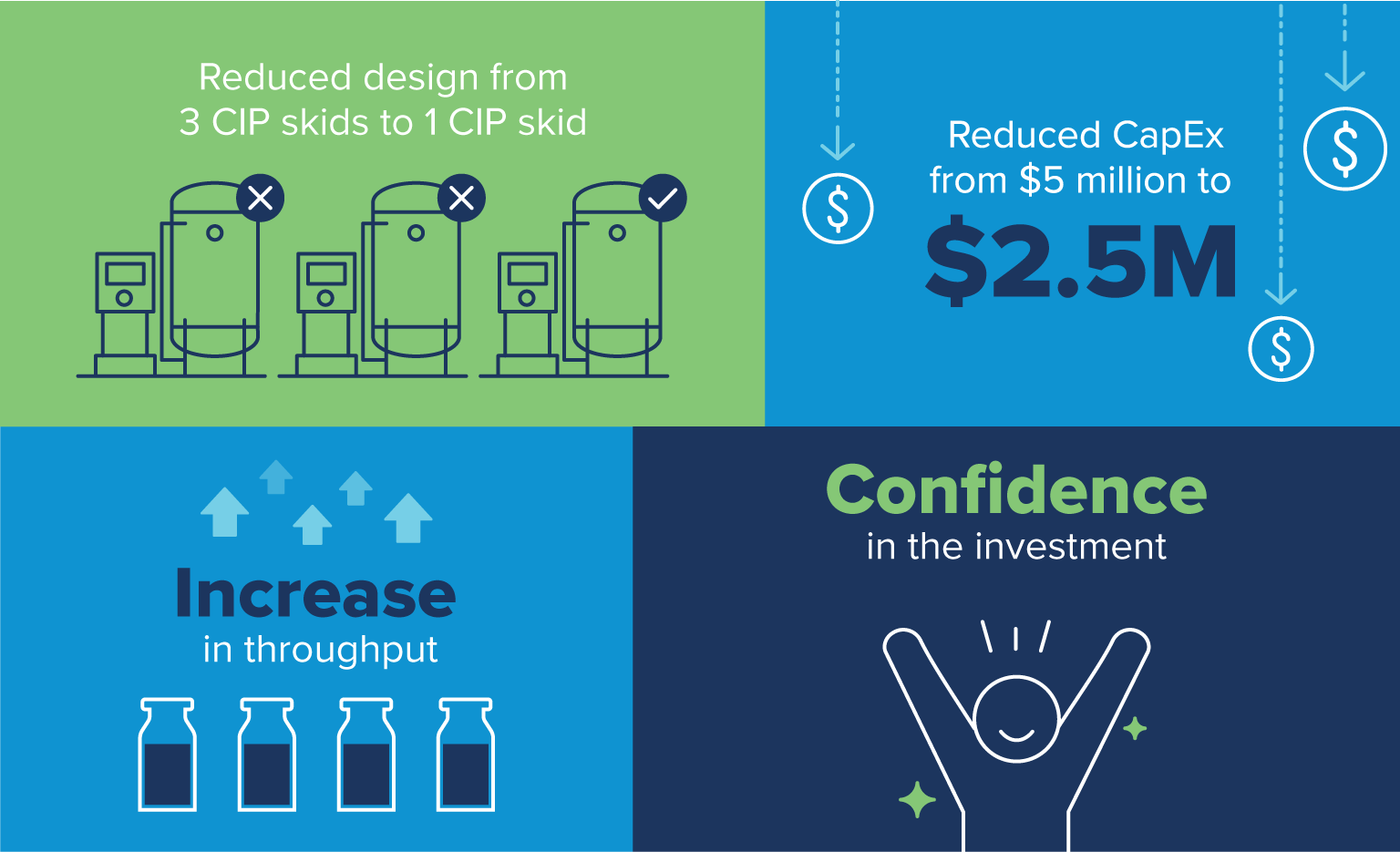
Process simulations provide a low-risk option to evaluate the need, process, and performance of new equipment prior to substantial capital investments. In addition, CRB’s industry experience allows us to critically assess processes and recommendations to ensure their reliability and real-world alignment. Thanks to the curiosity and due diligence of this client’s project team, they were able to move forward with a design option that cut CapEx spending in half and save the company millions of dollars while still delivering an increased run rate.
This is just one recent example of how our process simulation engineers can support leaner business decisions. If you are adding, replacing, or modifying the equipment in your process and want assurance in your investment, talk with our Process Simulation Engineers first.