
Operational improvement as the gateway to efficient ATMP production
Even a minor operational improvement can generate major benefits for ATMP manufacturers, particularly when personalized therapies are involved. Unlock these benefits in your own facility by using the tools of operational improvement to answer six mission-critical questions.
This is the third installment in our series, “The ATMP Manufacturer’s Guide to Commercialization and cGMP Compliance.” For early access to future articles in this series, sign up here.
Scaling your ATMP operation to commercial volumes can feel like playing a game of three-dimensional chess. To succeed, you need to think several moves ahead, ensuring that your day-to-day manufacturing activities are suitable for a standardized cGMP manufacturing platform and a resilient automation strategy—two key enablers of commercialization which we discussed in previous installments of this series.
In this article, we’re moving out of day-to-day manufacturing and into the bigger picture of your facility, where the principles of operational improvement come into play.
Operational improvement is about deeply understanding what’s happening inside your facility, from the warehouse to the production suites to the QC lab, and using that understanding to streamline workflows, reduce costs, and accelerate production. The net result is a leaner facility that operates not as a series of standalone operations but as a harmonized and highly efficient whole.

- How do we align production capacity with demand?
- What are your equipment needs?
- How can you prepare for planned and unplanned interruptions?
- How can you streamline your manual steps and facility pathways?
- How can you build more efficiency into your warehousing and storage areas?
- How can you prepare your QC lab for just-in-time testing and release?
No matter what you’re manufacturing in your ATMP facility, you face these questions. But there’s one category of ATMP manufacturing where the answers are especially difficult to uncover: personalized therapies.
If you fall into this category, then you need a facility capable of delivering a large number of very small, individualized product batches. That means scaling out, not up, which magnifies your operational complexity and potentially constricts your ability to stay lean, efficient, and cost-effective.
This is the perfect scenario in which to highlight the advantages of operational improvement. Through the lens of personalized medicine, all ATMP manufacturers can see how to leverage operational improvement to address complexity, manage variability, and accelerate outcomes.
What are the tools of process optimization and operational improvement?
Digital twin → The digital twin is a computational model that replicates your facility, your processes, and the real-world variables that impact your outcomes.
Modeling and simulation → Think of the digital twin like a GPS device, accurately representing a specific real-world environment and the shifting dynamics that impact how you move through it at any given time. Simulation, then, is the process of plugging a destination into that GPS to uncover the most optimized route.
This is one of the most impactful ways to optimize your process early and make high-impact, future-proof decisions about your facility, your workforce, and your overall manufacturing, warehousing, and QC strategies, both today or far into the future.
Discrete event simulation (DES) models → This modeling sub-type is suitable for scenarios that involve a degree of uncertainty and randomness, making it particularly useful for manufacturers of personalized medicine. From shifting demand to the impacts of manual process interventions, you face immense variability; DES models can help you characterize that variability and develop robust, optimized manufacturing strategies in response to it.
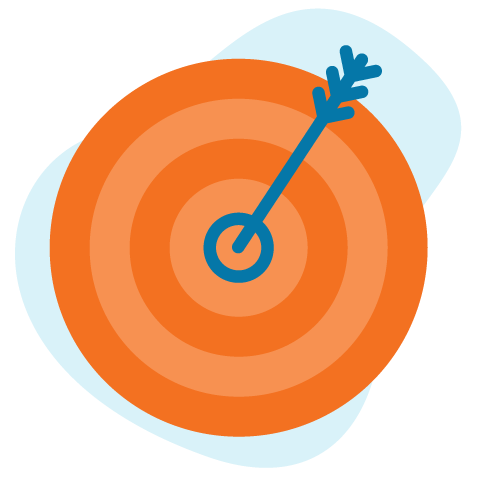
1. How do we align production capacity with demand?
Manufacturers across industries face the same fundamental question: what will production demand look like in the future, and how much capacity do we need to meet that demand?
Some manufacturers keep demand and capacity in balance by feeding their factories with waitlisted orders, giving them the runway to handle market fluctuations while operating at full capacity.
If your facility manufactures personalized medicine, you don’t have that luxury. When a patient needs a therapy, they need it now, not in six months. To meet that need, the key is to prepare for variability on multiple levels.
Variability in your production demand is a real and ongoing challenge.
The volume of patients seeking your product is likely to vary significantly across a year, a month, or even from week to week. This puts you at risk of having too much capacity at one time and too little at another, impacting both your manufacturing costs, the cost to patients, and the speed at which your products reach the bedside.
Your starting material is also highly variable.
There are many steps involved in moving your starting material from the patient’s bedside to the production facility. Several of those steps happen upstream of your facility, which limits your control and leaves you vulnerable to delays. Even a small delay can have a cascading effect on your overall production timeline.
Once you’ve received that starting material, you face another challenge. Your manufacturing times and other process boundaries could be impacted by the quality of that starting material. Several factors play a role in determining that level of quality, and you can’t control most of them—but you can plan for them using the tools of operational improvement.
Use process modeling to incorporate variability into your manufacturing plan.
By leveraging discrete event simulation (DES) models, you can characterize the uncertainties that impact your operation, including shifts in the volume of incoming patient material and changes in production time based on the quality of that material. This will give you the insights you need to walk the narrow line between too much capacity and too little, enabling you to handle variability smoothly from one end of your facility to another.

2. What are your equipment needs?
There are two answers to this question: the simple one, and the right one.
The simple answer looks at your target throughput and works out what you’ll need to meet that target, with the assumption that your equipment and your personnel will operate at maximum productivity. But that calculation is incomplete. What about cleaning or maintenance activities? What about unexpected downtime? What about the activities that take personnel away from active work, such as training sessions or administrative tasks?
To reach the right answer, you need an approach that recognizes how each of these factors and variables impacts the next, and what that means for your overall operation.
To guarantee operations, don’t plan for one hundred percent equipment utilization.
A robust equipment utilization strategy includes a conservative margin for handling planned and unplanned downtime and other events that could impact the total run hours of your equipment and your overall facility.
The tools of operational improvement will help you to estimate that margin. Through modeling and simulation, for example, you can closely observe all the interdependent factors that impact production, from equipment maintenance schedules to the productivity of your personnel. With those insights in hand, you can fine-tune your estimation of equipment and personnel needs, and plan an appropriate number of production lines. Getting to that answer isn’t simple, but it’s the right approach if you want accurate estimates.
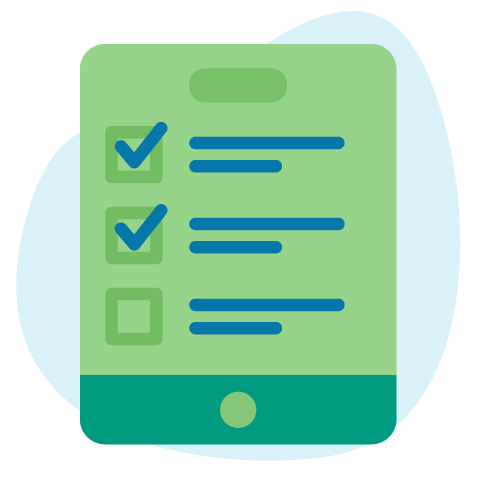
3. How can you prepare for planned and unplanned interruptions?
In the section above, we explored the importance of building redundancy into your equipment and personnel plan in order to guarantee operations, even in the face of interruptions. Understanding where those interruptions might come from—and how to minimize their scale and frequency—is equally important, and can help you further maximize your equipment utilization.
Take a proactive approach to maintenance.
By feeding a process model with as much historical manufacturing data as possible, you can quantify your system’s robustness and determine the statistical likelihood of equipment failures and other exceptional events. With this information, you can not only plan preventative maintenance activities—you can also schedule that maintenance at optimal times, helping to minimize downtime and reduce overall impacts on operations.
Prepare for unplanned events.
The risk of an unplanned interruption will decrease with this proactive, data-driven approach to preventative maintenance, but it won’t entirely disappear—and that’s where a deep understanding of your process, enabled by the tools of operational improvement, pays off even further.
With the right optimization strategies in place, you’ll be more sensitive to even small changes or deviations in production results, helping you to proactively raise an alert and increase your opportunity to take action. Early warning of an unplanned event could also help you avoid a process deviation and, in the worst cases, the loss of valuable products—an especially devastating possibility when a single batch could be a patient’s last hope.
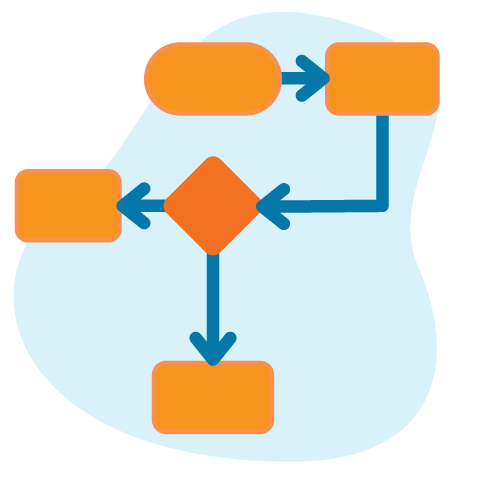
4. How can you streamline all manual steps and facility pathways?
Automated technology is the key to commercial feasibility, particularly in the field of personalized medicine. Still, even the most automation-friendly manufacturers will have to contend with manual steps. Perhaps the technology needed to automate those steps is not yet available. Perhaps you don’t have the capital to integrate that technology right away. Whatever the reason for a manual intervention, its consequences can be far-reaching—and those consequences get magnified as you scale your workforce to meet the demands of commercial manufacturing.
First, there are the obvious implications: the more skilled operators you need, the more time and money you’ll have to invest in recruiting, training, and compensating those operators, as well as the administrative staff needed to support them. Then there’s the problem of facility infrastructure. You’ll need to right-size not just your production spaces to accommodate adequate personnel, but your support and amenity spaces as well, including locker rooms, break areas, and parking lots. Even if you have the resources to operate a suitable workforce and the space to accommodate it, you’ll be facing another challenge: the variability inherent to manual interventions.
The tools of operational improvement can help you understand and minimize all of these challenges.
Quantify and mitigate the variability involved in manual operations.
Process modeling and simulation can help you understand the relationship between each manual step and your production line’s overall efficiency at scale, how those steps impact the reproducibility of results, and where you can optimize your process by eliminating redundant activities or integrating automation to replace or accelerate operator-driven tasks.
Use process modeling to right-size your headcount.
Through modeling and simulation, you can develop a deep, data-driven understanding of the manual steps in your process. To reach that understanding, you’ll rely on the same ecosystem of interdependent factors that we discussed earlier: your utilization targets, your target throughput, your estimated downtime, and so on. All of these components relate to and depend on each other; your model will allow you to examine these relationships in real-time, which will help you determine how many operators you need to support ongoing operations.
This, in turn, will help you to plan a facility that will adequately and efficiently accommodate your workforce.
Simplify your facility layout to increase efficiency and reduce manual interventions.
The way your facility is designed can greatly impact the speed and efficiency of each manual step in your process. You can use this fact to your advantage by leveraging the tools of operational improvement to simulate and optimize travel distances through a new facility, or to identify opportunities for better organization in an existing environment.
For example, moving a product sample from the cGMP cleanroom to the QC lab can be a lengthy step involving multiple personnel, especially when time-critical IPC tests are required. When that step is inefficiently designed—if no personnel is immediately available to receive the sample through an airlock and transport it to the lab, or if the cGMP space and the lab are located at different ends of the facility—it can hold up the whole production process.
Simulations can help identify these potential bottlenecks and road-test possible solutions, giving you the opportunity to rethink the way your facility is organized, from its overall layout down to the placement of specific equipment within a room. This can improve overall efficiency while potentially reducing your required headcount.
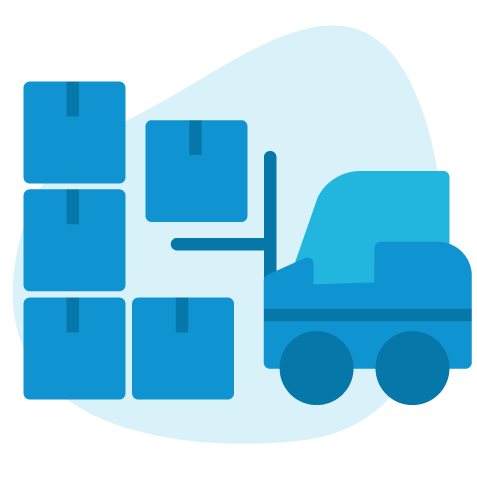
5. How can you build more efficiency into your warehousing and storage areas?
At the beginning of this article, we said that operational improvement helps to establish a harmonized whole out of a series of standalone operations. That includes a facility’s warehouse and storage areas. By applying the tools of operational improvement to understand the pathway from the warehouse to the production suite, you can make that pathway much shorter, simpler, and more efficient.
Plan from the inside out, starting with a Bill of Materials.
Use your process model to capture and document every material required to make one batch of your product. This is the basis for your Bill of Materials (or BOM), which documents the materials required to run your process a single time.
By leveraging insights that you’ve already developed—including potential variability in demand, expected utilization rates, and other key production metrics—you can use that BOM to calculate exactly which materials you will need and when, how much storage space (and what type of storage) you’ll need to accommodate those materials in each work center, and which pathways those materials will follow as they travel through the kitting process and are released into cGMP production.
Establishing this plan early gives you the opportunity to optimize each logistical step across the warehouse and kitting process, ensuring that you’ve capitalized on every opportunity to streamline your warehousing process.

6. How can you prepare your QC lab for just-in-time testing and release?
As manufacturers scale their process from R&D into the commercialized, cGMP-proof environment, the volume of samples moving through the QC lab increases proportionally. Without proper planning, this shift in volume can quickly drive your manufacturing areas and your QC lab out of sync. As a result, bottlenecks increase and manufacturing costs soar.
The solution is to develop an appropriate QC strategy that’s tailored for the needs of your particular ATMP modalities. This is doubly important if you’re manufacturing personalized therapies, because you can’t wait weeks or months for testing and release the way products in more conventional pharmaceutical facilities can. That QC strategy needs to lay the groundwork for a fast, responsive, and intensely efficient lab, designed around data-driven insights generated by the tools of operational improvement.
The same principles of process optimization applied in the manufacturing suite can impact the QC lab.
Predicting variable demand, establishing equipment and utilization rates, optimizing operator headcount, and anticipating maintenance needs—all of these considerations, which we discussed above in the context of the manufacturing environment, apply in the QC lab, as well.
By simulating the QC process in a digital environment, you can examine each of these considerations and identify opportunities to reduce the time required for sample testing and product releases. This will position your QC lab to offer responsive, just-in-time testing so that production lines can continue running with minimal interruptions or wait times. Overall production time will likely decrease as a result, as will manufacturing costs, both of which ultimately benefit the patient waiting for a critical therapy.
Operational improvement is about more than good business.
The key to winning at three-dimensional chess is to understand the game as completely as possible. In the business of ATMP manufacturing, that means knowing exactly what’s happening inside and outside of your facility, as well as what will happen as your operation scales, your pipeline expands, and the number of patients who rely on your output grows.
To develop and maintain that depth of knowledge, apply the tools of operational improvement. They’re your gateway to improving efficiency, addressing variability, and planning for a successful commercial future. From a business perspective, this makes good sense; from the perspective of patients who rely on the therapies you’re manufacturing, this makes life possible.
Are you interested in speaking with our operational improvement experts? Let´s Talk!